This machine is ideally installed directly in the production lines.
It has an extremely simple operating principle for the total elimination of defective cans (pin holes, dented flanges, cracked flanges, cracked welds, etc.). Standard vacuum degree is applied to cans and those found faulty will be automatically rejected.
Can height can be set with simple adjustments in about 30 minutes. Changeover of diameter is also possible by means of tool kits (setting in 50 minutes).
The infeed belt with screw feeds cans to the rotary testing unit with 20, 40 or 52 heads.
As each head completes a full revolution, it depressurizes the can being tested to a standard pressure value. Any variations detected in this depressurization mean there is a leak in the can, so the machine produces an electronic signal or ejects the can. After testing, the good cans are reinserted in the production line.
The machine is equipped with special pneumoelectronic transducer unit for detecting microholes. This device displays on the electronic board the number of the pocket in which a defect has been found. Set up is done automatically using a special soft key installed on the same panel.
The control panel controls and monitors the various operating phases of the machine, providing a rapid set-up of reference parameters and display of the current pressure values and reject counts for each rotary head.
Technical data (standard):
CAN DIMENSIONS
Model CVT20 CVT40 CVT52
diameter range (mm) 99 – 155 52 – 99 52 – 73
height range (mm) 35 – 260 35 – 260 35 – 260
OUTPUT
Model CVT20 CVT40 CVT52
operating speed 300 cpm 600 cpm 900 cpm
OPERATING TEST VACUUM (CVT20 – 40 – 52) 400 mBar – 500 mBar
ELECTRICAL REQUIREMENTS (CVT20 – 40 – 52) 5 Kw, 380 V, 50 Hz, 3-phases + neutral wire
AIR CONSUMPTION 50 l/minute at 6 Bar
Upon request the machine can be customized
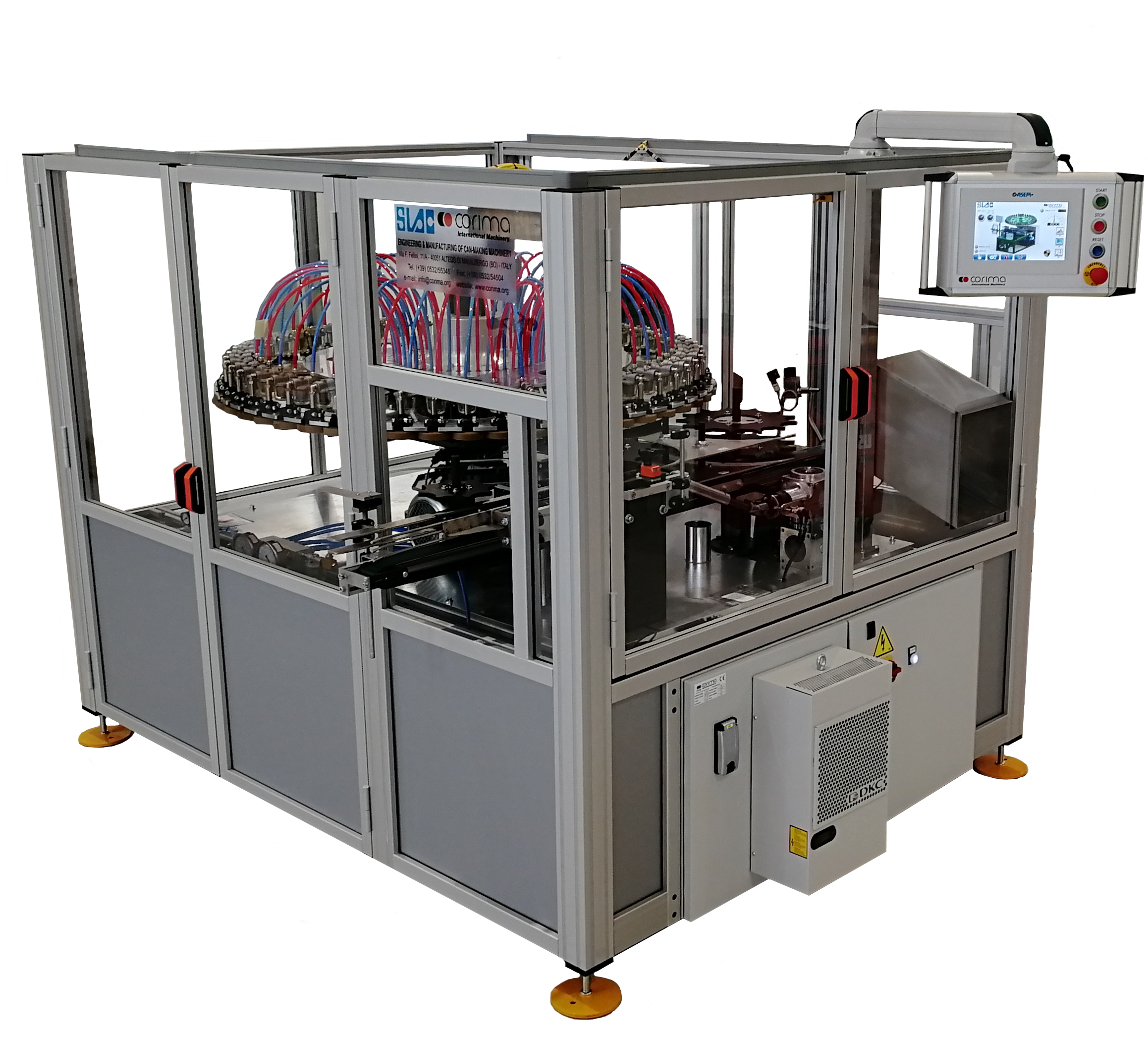
“A network of companies with acquired experience and know-how”